Understanding the Applications of Directional Control Valves
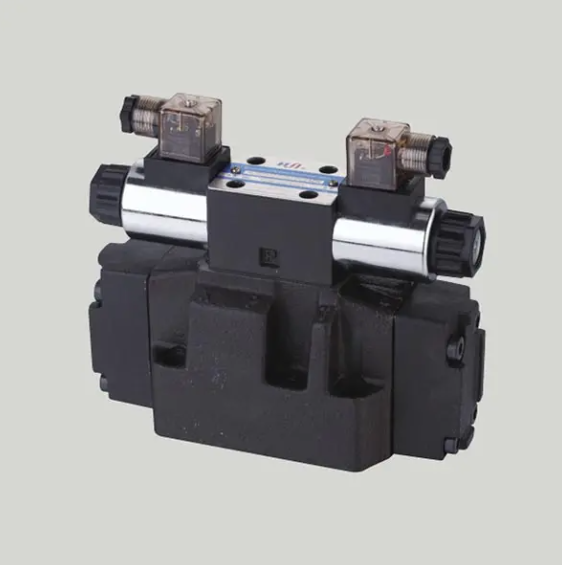
Types of Directional Control Valves
Understanding the different types of directional control valves is crucial for selecting the right one for your application. Each type serves a unique purpose and offers specific functionalities.
Two-way Valves
Functionality of Two-way Valves
Two-way valves are the simplest form of directional control valves. They have two ports, allowing fluid to flow in or out. You can use them for basic on/off fluid supply applications. When you need to start or stop the flow of fluid, a two-way valve is your go-to option.
Applications of Two-way Valves
These valves are commonly used in systems where you need to control the flow of fluids in a straightforward manner. For instance, they are ideal for applications that require a simple open or closed state, such as in water supply systems or basic hydraulic circuits.
Three-way Valves
Functionality of Three-way Valves
Three-way valves have three ports and are designed to direct fluid between two different paths. They are often used in applications where air needs to be alternately applied and released. This makes them suitable for controlling single-acting cylinders.
Applications of Three-way Valves
In industrial settings, three-way valves are essential for automation, material handling, and packaging. They allow precise control over actuator positioning, enhancing both efficiency and safety. You will find them in assembly lines where managing actuator movement is critical.
Four-way Valves
Functionality of Four-way Valves
Four-way valves are more complex, featuring four ports. They are used to pressurize and exhaust two ports interdependently. This functionality is crucial for controlling double-acting actuators. A 3-position, 4-way valve can stop an actuator or allow it to float, making it versatile for various applications.
Applications of Four-way Valves
These valves are prevalent in both air and hydraulic circuits. You will see them in aerospace applications, where precise control over actuator movement is necessary. They are also common in industrial machinery, where they help manage complex hydraulic systems.
Applications of Directional Control Valves in Various Systems
Industrial Machinery
Use in Manufacturing Equipment
In manufacturing equipment, directional control valves are indispensable. You use them to manage the flow of hydraulic fluid, ensuring precise control over machinery operations. These valves allow you to start and stop machines efficiently, enhancing productivity. By directing fluid flow, they help maintain the desired speed and force, which is crucial for tasks like cutting, pressing, and molding. The integration of digital technology in these valves has made them more intelligent and adaptable, meeting the demands of modern Industry 4.0 environments.
Role in Automation Systems
Automation systems rely heavily on directional control valves. You find these valves essential for controlling the movement of automated machinery. They enable you to achieve precise positioning and timing, which are vital for tasks such as assembly and packaging. By using these valves, you can enhance the efficiency and safety of automated processes. The evolution of electro-hydraulic control valves has further improved their performance, making them more reliable and energy-efficient.
Automotive Systems
Application in Vehicle Hydraulics
In vehicle hydraulics, directional control valves play a crucial role. You use them to manage the flow of hydraulic fluid in systems like power steering and suspension. These valves ensure smooth and responsive vehicle handling, providing you with a comfortable driving experience. By controlling the direction and pressure of fluid flow, they help maintain stability and safety on the road.
Use in Brake Systems
Directional control valves are vital components in automotive brake systems. You rely on them to regulate the hydraulic pressure applied to the brakes. This ensures that your vehicle stops effectively and safely. By directing fluid flow, these valves help distribute braking force evenly, preventing skidding and enhancing control during emergency stops.
Aerospace Applications
Function in Aircraft Control Systems
In aircraft control systems, directional control valves are essential. You use them to manage the movement of control surfaces, such as flaps and rudders. These valves ensure precise control over the aircraft’s direction and stability. By directing hydraulic fluid to the appropriate actuators, they help you maintain safe and efficient flight operations.
Use in Spacecraft Mechanisms
Spacecraft mechanisms also depend on directional control valves. You find these valves crucial for controlling the movement of various components, such as solar panels and robotic arms. By managing fluid flow, they ensure that these components operate smoothly and reliably in the harsh conditions of space. The advancements in digital hydraulic technology have made these valves more robust and reliable, enhancing the safety and longevity of spacecraft systems.
Medical Devices
In the realm of medical devices, directional control valves are indispensable. You use them to manage the flow of compressed air and fluids, ensuring precise control over medical equipment. These valves play a vital role in devices like ventilators and anesthesia machines, where accurate fluid control is crucial for patient safety. By directing the flow of air or liquid, you can maintain the desired pressure and volume, which is essential for effective treatment. The integration of digital technology in these valves has enhanced their reliability and efficiency, making them more adaptable to the evolving needs of modern healthcare.
Construction and Agricultural Equipment
Directional control valves are essential in construction and agricultural equipment. You rely on them to operate various attachments and implements, such as loaders, excavators, and plows. These valves allow you to control the movement and force of hydraulic systems, enabling efficient operation of heavy machinery. By directing fluid flow, you can adjust the speed and direction of attachments, enhancing productivity and precision. The advancements in digital hydraulic technology have made these valves more robust and energy-efficient, meeting the demands of challenging work environments.
Robotics
In robotics, directional control valves are crucial for managing the movement of robotic arms. You use these valves to control the flow of hydraulic or pneumatic fluid, ensuring precise positioning and motion. By directing fluid to the appropriate actuators, you can achieve smooth and accurate arm movements, which are essential for tasks like assembly, welding, and material handling. The evolution of electro-hydraulic control valves has improved their performance, making them more reliable and adaptable to the complex requirements of robotic systems.
Oil and Gas Industry
Control of Fluid Flow in Drilling and Extraction
In the oil and gas industry, you rely on precise control of fluid flow during drilling and extraction processes. Directional control valves play a pivotal role in managing these operations. By directing the flow of hydraulic fluids, you can ensure that drilling equipment operates efficiently and safely. These valves help you maintain the desired pressure and flow rate, which are crucial for effective drilling and extraction.
-
Drilling Operations: During drilling, you need to manage the flow of drilling mud and other fluids. Directional control valves allow you to adjust the flow rate and pressure, ensuring that the drill bit operates at optimal efficiency. This control helps prevent blowouts and other drilling hazards, enhancing safety and productivity.
-
Extraction Processes: In extraction, controlling the flow of fluids is essential for maintaining well pressure and optimizing recovery rates. You use directional control valves to regulate the flow of oil, gas, and water, ensuring that extraction processes run smoothly. By managing fluid flow, you can maximize resource recovery while minimizing environmental impact.
-
Advanced Technologies: The integration of digital hydraulic technology has revolutionized fluid control in the oil and gas sector. Digital On/Off valves offer several advantages, including higher robustness, lower energy consumption, and increased safety. These valves are less sensitive to contamination, making them ideal for harsh environments. Their ability to connect easily with computers and PLCs enhances their flexibility and reliability.
Scientific Research Findings: Advancements in digital hydraulic technology have led to simpler and more cost-effective valves. These innovations provide higher safety and reliability, crucial for the demanding conditions of the oil and gas industry.
By utilizing these advanced control systems, you can improve the efficiency and safety of drilling and extraction operations. The evolution of electro-hydraulic control valves continues to meet the industry’s growing demands, ensuring that you can adapt to new challenges and opportunities.
Directional control valves are vital in various systems, ensuring efficient fluid management. You have explored their types and applications, from simple two-way valves to complex four-way configurations. Each type serves a unique purpose, enhancing the functionality of hydraulic and pneumatic systems. Choosing the right valve is crucial for optimal performance. As an expert in hydraulic systems notes, “Directional control valves regulate the flow and direction of fluid in the circuit.” This highlights their importance. By understanding these components, you can ensure reliability and efficiency in your applications.