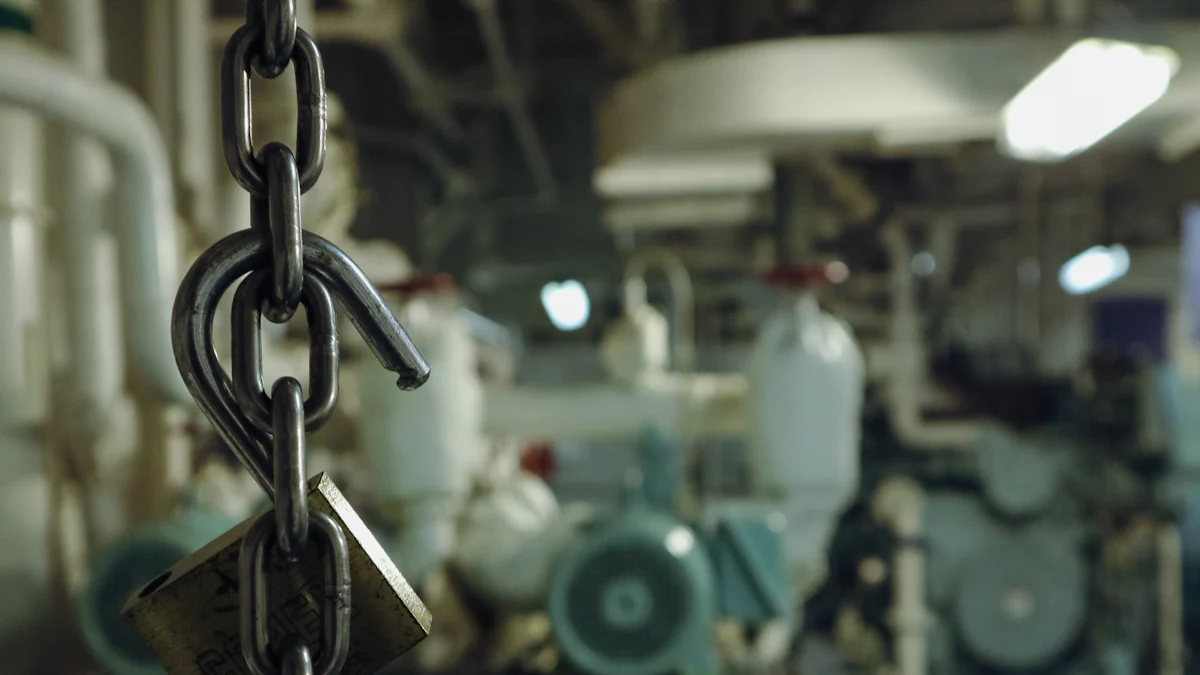
The top 10 industrial hydraulic valve factories are at the forefront of transforming modern industries. Advancements in this field are driving innovation across sectors such as oil and gas, robotics, and automation. The integration of cutting-edge technologies, including digital hydraulics and electrohydraulic systems, has significantly enhanced valve performance. For example, the global hydraulic valves market is anticipated to reach $5.89 billion by 2024, underscoring its growing significance. These developments not only boost efficiency but also support sustainability, ensuring adherence to global standards. Companies like Ningbo Hanshang Hydraulic Co., Ltd. exemplify this progress, blending precision engineering with eco-conscious practices.
Key Takeaways
- Embrace IoT integration: Smart valves with IoT capabilities enhance performance and enable real-time monitoring, leading to improved efficiency and reduced downtime.
- Prioritize energy efficiency: Adopting digital hydraulic technology and low-pressure drop valves can significantly lower energy consumption and operational costs.
- Focus on customization: Tailoring hydraulic valves to meet specific industry needs ensures optimal performance and reliability in diverse applications.
- Leverage advanced simulation software: Utilizing virtual prototyping accelerates product development and minimizes costs by identifying design issues early.
- Adopt eco-friendly practices: Implementing sustainable materials and processes not only meets regulatory standards but also enhances brand reputation.
- Utilize additive manufacturing: 3D printing allows for rapid prototyping and the production of complex components, driving innovation and reducing waste.
- Implement digital twin technology: This approach enables real-time monitoring and predictive maintenance, optimizing performance and extending equipment lifespan.
Smart Valves and IoT Integration in Top 10 Industrial Hydraulic Valve Factory
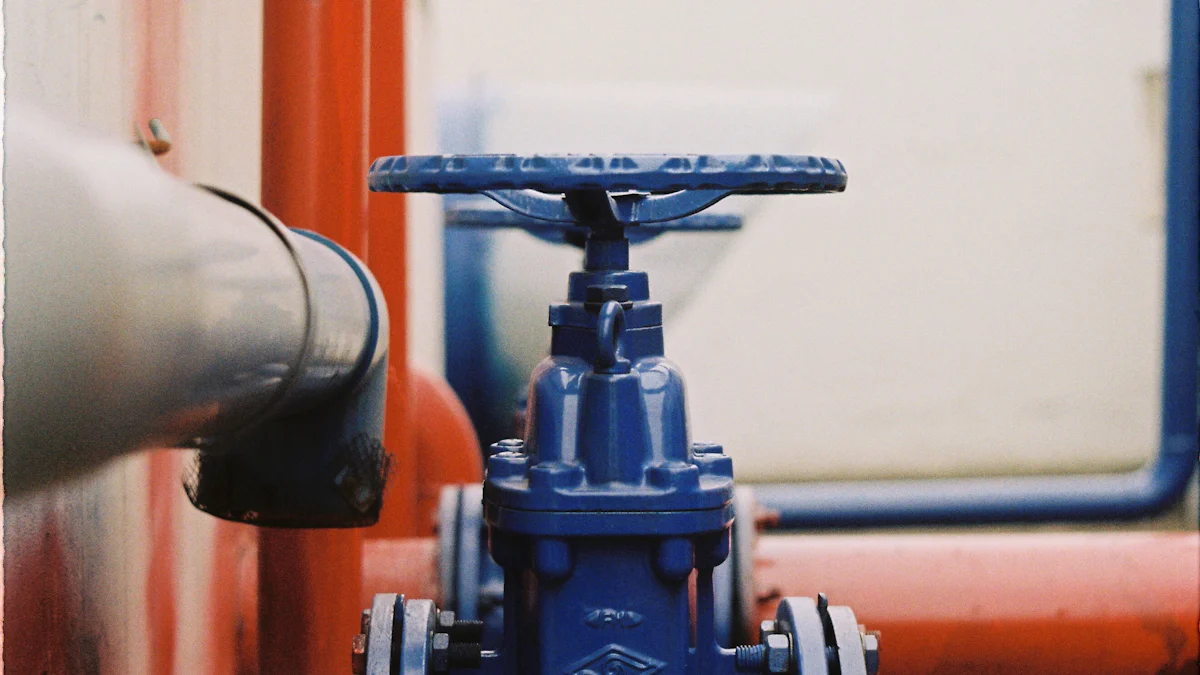
The rise of smart valves has revolutionized the hydraulic valve industry. These advanced systems, powered by the Internet of Things (IoT), are transforming how industries operate. By integrating connectivity and intelligence, the hanshang hydraulic leaders are setting new benchmarks for performance and efficiency.
Enhanced Performance Through Connectivity
Smart valves equipped with IoT capabilities enable seamless communication between hydraulic systems and central control units. This connectivity ensures that every component works in harmony, optimizing overall system performance. For instance, electro-hydraulic control valves, now more digital and intelligent, align perfectly with Industry 4.0 standards. These valves incorporate advanced sensors and data analytics, which allow operators to monitor and adjust performance in real time.
The hanshang hydraulic manufacturers have embraced this trend by embedding communication features into their products. This innovation not only enhances precision but also reduces downtime. Operators can now identify inefficiencies instantly and address them without halting operations. This level of connectivity has become a game-changer for industries like aerospace, robotics, and oil and gas.
Real-Time Monitoring and Predictive Maintenance
IoT integration has introduced real-time monitoring capabilities to hydraulic systems. Sensors embedded in smart valves continuously collect data on pressure, temperature, and flow rates. This data is then transmitted to centralized systems, where it is analyzed to detect anomalies. Predictive maintenance becomes possible as these systems can forecast potential failures before they occur.
For example, the electro-hydraulic servo valve market has seen significant growth due to its ability to integrate predictive maintenance features. These valves use IoT to provide actionable insights, helping industries avoid costly breakdowns. By addressing issues proactively, companies can extend the lifespan of their equipment and reduce operational costs.
Ningbo Hanshang Hydraulic Co., Ltd., a pioneer in hydraulic valve manufacturing, exemplifies this approach. With state-of-the-art facilities and a commitment to innovation, the company has adopted IoT-driven solutions to enhance product reliability. Their focus on real-time monitoring and predictive maintenance ensures that their hydraulic systems meet the highest standards of efficiency and durability.
Integration of Electronics in Hydraulic Systems
The integration of electronics into hydraulic systems has redefined precision and efficiency in industrial applications. This trend has gained momentum as industries demand more accurate and reliable solutions to meet evolving operational challenges. By combining electronic controls with hydraulic mechanisms, manufacturers have unlocked new possibilities for performance optimization.
Combining Electronics and Hydraulics for Precision
Electronics have transformed traditional hydraulic systems by introducing advanced control capabilities. Unlike conventional setups, electro-hydraulic systems incorporate electronic components that enable precise control over pressure, flow, and movement. This combination ensures unparalleled accuracy in operations, making it ideal for industries like aerospace, robotics, and manufacturing.
Electro-hydraulic systems also offer significant advantages in terms of power density and maintenance. These systems pack more power into a smaller footprint, allowing for compact designs without compromising performance. Maintenance becomes simpler due to reduced external leaks, which also enhance cleanliness and safety. For example, the hanshang hydraulic leaders have adopted these systems to deliver high-performance solutions tailored to modern industrial needs.
Moreover, the versatility of electro-hydraulic systems allows them to operate efficiently in diverse environments. Their ability to handle shock loading while maintaining stability makes them a preferred choice for demanding applications. This level of precision and adaptability has set a new standard in hydraulic valve manufacturing.
Benefits of Electro-Hydraulic Actuation
Electro-hydraulic actuation has emerged as a game-changer in the hydraulic valve industry. By integrating electronic controls, these systems provide smoother and more responsive actuation compared to traditional methods. This responsiveness translates into faster operation cycles and improved productivity.
One of the key benefits of electro-hydraulic actuation lies in its energy efficiency. These systems optimize power usage by delivering energy only when needed, reducing overall consumption. This feature aligns with the growing emphasis on sustainability in industrial operations. Additionally, the reduced energy requirements contribute to cost savings, making these systems an economical choice for businesses.
Another advantage is the enhanced safety offered by electro-hydraulic systems. The integration of electronics minimizes the risk of mechanical failures, ensuring reliable performance even under extreme conditions. Industries that prioritize safety, such as oil and gas or heavy machinery, have increasingly turned to these systems for their operations.
Ningbo Hanshang Hydraulic Co., Ltd. exemplifies the successful adoption of electro-hydraulic technology. With state-of-the-art facilities and a commitment to innovation, the company has developed hydraulic valves that combine precision engineering with electronic advancements. Their focus on delivering high-quality solutions reflects the broader industry trend toward integrating electronics in hydraulic systems.
Focus on Environmental Compliance in Hydraulic Valve Manufacturing
Meeting Global Emission Standards
I have observed that environmental regulations are becoming stricter across industries. Manufacturers now face increasing pressure to meet global emission standards. In hydraulic valve manufacturing, this means designing products that minimize fugitive emissions. These emissions, often caused by leaks in valve stem-seals, can release hazardous gases into the atmosphere. To address this, manufacturers have adopted advanced sealing technologies and rigorous testing protocols.
For example, standards like ISO 15848-1 and API 624 mandate fugitive emission testing for valves used in refining and upstream processes. These standards ensure that valves meet stringent requirements for leak prevention. However, midstream applications still lack clear guidelines, creating challenges for manufacturers. Despite this, companies like Ningbo Hanshang Hydraulic Co., Ltd. have taken proactive steps. By implementing precise engineering and quality control measures, they ensure their valves comply with the highest environmental standards.
The integration of variable valve timing has also emerged as a key strategy. This technology optimizes valve operation, reducing emissions while improving performance. It aligns with the industry’s commitment to sustainability and regulatory compliance. I believe that meeting these standards not only benefits the environment but also enhances the reputation of manufacturers in the global market.
Adoption of Eco-Friendly Materials and Processes
The shift toward eco-friendly materials and processes has gained momentum in hydraulic valve manufacturing. I have noticed that companies are increasingly using sustainable materials to reduce their environmental footprint. For instance, many manufacturers now prefer recyclable metals and low-impact coatings for valve production. These materials not only meet environmental standards but also improve product durability.
In addition to materials, the manufacturing processes themselves have evolved. Advanced technologies like additive manufacturing (3D printing) enable precise production with minimal waste. This approach supports sustainability by reducing material consumption and energy usage. At Ningbo Hanshang Hydraulic Co., Ltd., we have embraced such innovations. Our state-of-the-art facilities utilize high-precision equipment to ensure efficient and eco-conscious production.
Furthermore, adopting energy-efficient practices has become a priority. Many factories now use renewable energy sources and implement energy-saving measures in their operations. These efforts align with global initiatives to combat climate change. By focusing on eco-friendly practices, manufacturers not only comply with regulations but also contribute to a greener future.
“Sustainability is no longer optional; it is a necessity for businesses aiming to thrive in today’s competitive landscape.” This quote resonates deeply with me as I witness the hydraulic valve industry embracing environmental responsibility.
Use of Advanced Simulation Software in Hydraulic Valve Design
The use of advanced simulation software has revolutionized hydraulic valve design. I have seen how this technology accelerates development and enhances precision. By simulating real-world conditions, manufacturers can refine designs before physical production begins. This approach minimizes risks and ensures optimal performance.
Virtual Prototyping for Faster Development
Virtual prototyping has become a cornerstone of modern hydraulic valve design. Engineers now rely on simulation tools to create digital models of valves. These models replicate real-world behavior under various conditions. For instance, numerical models developed in environments like Simulink demonstrate how valves perform at different flow rates and pressure drops. One study showed a maximum flow rate of 70 L/min with a pressure drop of 10 bar, highlighting the accuracy of these simulations.
This process eliminates the need for multiple physical prototypes. It reduces the time required to bring a product to market. I believe this efficiency is crucial for staying competitive in the fast-paced industrial sector. The top 10 Industrial hydraulic valve factory leaders have embraced virtual prototyping to streamline their development cycles. By doing so, they deliver innovative solutions faster and more effectively.
Virtual prototyping also allows for testing under extreme conditions. Engineers can simulate high-pressure environments or rapid temperature changes. This capability ensures that valves meet stringent industry standards. It also provides confidence in the reliability of the final product.
Reducing Costs and Errors Through Simulation
Simulation software not only speeds up development but also cuts costs. Traditional methods often involve trial-and-error testing with physical prototypes. This approach can be expensive and time-consuming. By contrast, simulations identify potential issues early in the design phase. Engineers can address these problems before production begins, saving both time and resources.
For example, simplified real-time models of hydraulic valves streamline the modeling process. These models use characteristic data acquisition and curve reproduction to predict valve behavior accurately. This method reduces errors and ensures that designs align with performance expectations. I have observed how this precision minimizes costly revisions during manufacturing.
Simulation tools also enhance accuracy in complex designs. Advanced software incorporates flow coefficient fitting formulas to optimize valve spool performance. These formulas, based on exponential functions, provide reliable results under various working conditions. This level of detail ensures that valves operate efficiently in diverse applications.
At Ningbo Hanshang Hydraulic Co., Ltd., we leverage state-of-the-art simulation technologies to refine our products. Our commitment to precision engineering reflects the broader industry trend toward digital innovation. By adopting these tools, we maintain our position as a leader in hydraulic valve manufacturing.
“Simulation is not just a tool; it is a necessity for modern engineering.” This statement resonates with me as I witness the transformative impact of simulation software on hydraulic valve design.
Additive Manufacturing (3D Printing) in Hydraulic Valve Production
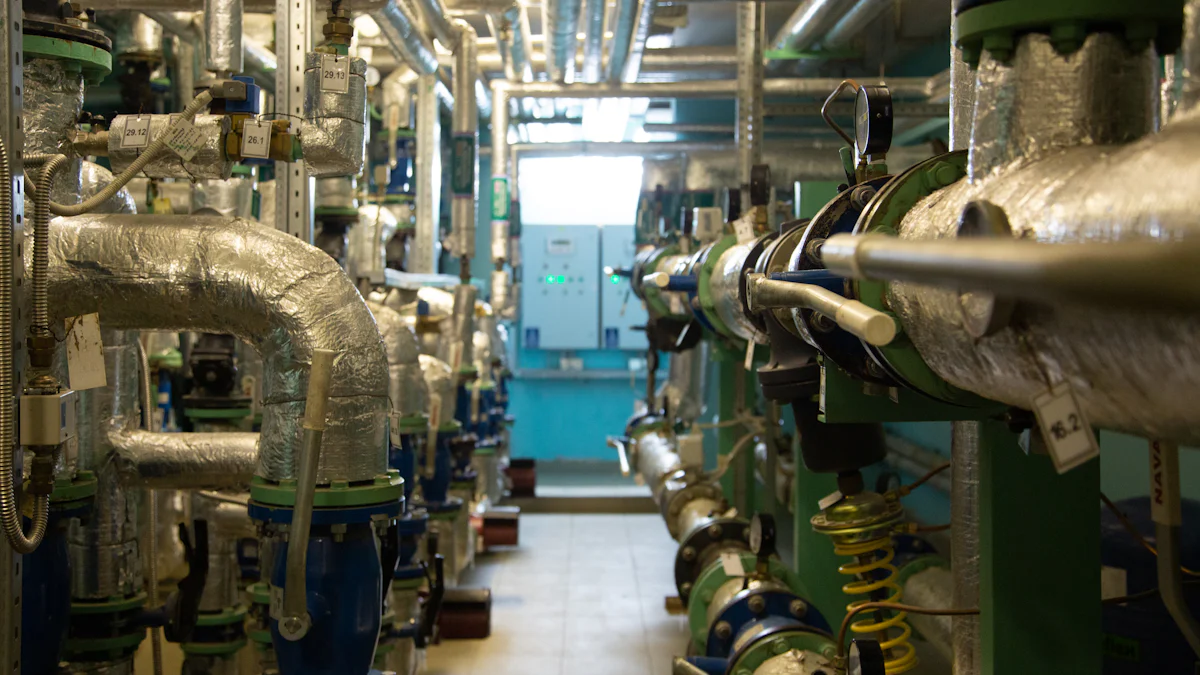
Customization and Rapid Prototyping
Additive manufacturing, commonly known as 3D printing, has transformed hydraulic valve production. I have observed how this technology enables manufacturers to create highly customized components with unmatched precision. Unlike traditional methods, 3D printing builds parts layer by layer, allowing intricate designs that were once impossible to achieve.
Customization has become a key advantage of 3D printing. Manufacturers can now tailor hydraulic valves to meet specific industry requirements. For example, industries like aerospace and robotics demand unique valve configurations to handle complex operations. With 3D printing, I can quickly design and produce prototypes that align perfectly with these needs. This flexibility ensures that each valve performs optimally in its intended application.
Rapid prototyping is another significant benefit. Traditional prototyping often involves lengthy processes and high costs. In contrast, 3D printing accelerates development by producing prototypes directly from digital models. This approach reduces lead times and allows for faster iterations. At Ningbo Hanshang Hydraulic Co., Ltd., we leverage this capability to refine our designs efficiently. By doing so, we ensure that our products meet the highest standards of quality and performance.
“3D printing is not just a manufacturing tool; it is a gateway to innovation.” This statement resonates with me as I witness how additive manufacturing drives creativity and efficiency in hydraulic valve production.
Cost-Effective Production of Complex Components
The cost-effectiveness of 3D printing has made it a game-changer in producing complex hydraulic valve components. Traditional manufacturing methods often struggle with intricate geometries, leading to higher material waste and production costs. Additive manufacturing eliminates these challenges by using only the necessary material to build each part.
For instance, metal 3D printing has gained traction in the hydraulic industry. This technology allows for the creation of lightweight yet durable components. By reducing material usage, manufacturers can lower production costs without compromising quality. I have seen how this approach benefits industries that require high-performance valves, such as oil and gas or heavy machinery.
Another advantage lies in the ability to consolidate multiple parts into a single component. Traditional methods often require assembling several pieces, increasing the risk of leaks or mechanical failures. With 3D printing, I can design and produce integrated components that enhance reliability and simplify maintenance. This innovation aligns with the industry’s push toward efficiency and sustainability.
At Ningbo Hanshang Hydraulic Co., Ltd., we embrace additive manufacturing to stay ahead in the competitive market. Our state-of-the-art facilities utilize advanced 3D printing technologies to produce complex components with precision. By adopting this approach, we deliver cost-effective solutions that meet the evolving demands of modern industries.
“Innovation thrives where technology meets necessity.” This quote perfectly captures the essence of 3D printing in hydraulic valve production. It empowers manufacturers to overcome challenges and unlock new possibilities.
Miniaturization of Hydraulic Valves for Modern Applications
Compact Designs for Space-Saving Applications
The demand for compact hydraulic valves has surged as industries prioritize space efficiency. I have observed how miniaturized designs address the challenges of limited installation areas. These valves, with their reduced size, fit seamlessly into tight spaces without compromising performance. This innovation proves essential in sectors like aerospace, robotics, and medical devices, where every inch of space matters.
Miniaturized digital hydraulic valves have emerged as a game-changer. These valves offer an energy-efficient alternative to traditional mono-stable switching valves. By reducing energy consumption, they align with the industry’s push for sustainability. I have seen how these compact designs enhance system efficiency while maintaining reliability. For example, advanced valve packages integrate multiple functionalities into a single unit, further optimizing space usage.
The development of torque motors in the 1950s by the MIT Dynamic Analysis and Control Laboratory laid the foundation for modern servo valve technology. Today, this legacy continues with miniaturized electro-hydraulic servo valves. These valves deliver precise control in applications requiring high accuracy. Their compact nature makes them ideal for industries like automation and military defense, where precision and space-saving solutions are critical.
At Ningbo Hanshang Hydraulic Co., Ltd., we embrace this trend by designing hydraulic valves that combine compactness with high performance. Our state-of-the-art facilities enable us to produce valves that meet the stringent requirements of modern applications. By focusing on miniaturization, we ensure that our products remain at the forefront of innovation.
Increased Demand in Robotics and Automation
The rise of robotics and automation has fueled the need for miniaturized hydraulic valves. I have witnessed how these valves play a pivotal role in enabling precise and efficient operations. Their small size allows integration into robotic arms and automated systems, enhancing functionality without adding bulk.
Digital hydraulic valves, despite initial challenges in practical implementation, now hold immense potential. Advances in computer technology have overcome earlier limitations, making these valves a viable solution for fluid power systems. Their ability to reduce energy consumption aligns perfectly with the goals of robotics and automation industries. I believe this innovation will revolutionize how machines operate, offering greater efficiency and control.
In robotics, miniaturized valves ensure smooth and accurate movements. They provide the precision needed for tasks like assembly, welding, and material handling. Automation systems benefit from their quick response times and reliability. These features make them indispensable in factories, warehouses, and other industrial settings.
Ningbo Hanshang Hydraulic Co., Ltd. recognizes the growing importance of robotics and automation. Our commitment to innovation drives us to develop hydraulic valves tailored to these applications. By combining miniaturization with advanced technology, we deliver solutions that meet the evolving demands of modern industries.
“Innovation thrives where precision meets efficiency.” This statement resonates with me as I see how miniaturized hydraulic valves transform industries, paving the way for a smarter and more efficient future.
Emphasis on Energy Efficiency in Hydraulic Systems
Reducing Power Consumption in Hydraulic Systems
Energy efficiency has become a critical focus in hydraulic systems. I have observed that traditional fluid power systems operate with an average efficiency of only 21%. This inefficiency leads to significant energy waste, as these systems consume between 2.25 and 3.0 quadrillion BTUs annually. Optimizing energy usage in hydraulic systems can drastically reduce this consumption.
One effective approach involves the adoption of digital hydraulic technology. Digital hydraulic valves, such as Digital Flow Control Units (DFCUs) and High-Frequency Switching Valves (HFSVs), have demonstrated their ability to minimize energy loss. These advanced architectures optimize flow control, ensuring that energy is used only when necessary. For instance, DFCUs address the limitations of traditional on/off valves by combining fast response speeds with improved flow rates. This innovation reduces energy consumption while maintaining system performance.
At Ningbo Hanshang Hydraulic Co., Ltd., we prioritize energy-efficient solutions in our product designs. Our hydraulic valves incorporate advanced engineering to minimize power usage without compromising functionality. By focusing on energy optimization, we help industries achieve their sustainability goals while reducing operational costs.
“Efficiency is not just about saving energy; it is about creating systems that perform better while consuming less.”
Development of Low-Pressure Drop Valves
Low-pressure drop valves play a pivotal role in enhancing energy efficiency. These valves reduce the resistance to fluid flow, which directly lowers the energy required to operate hydraulic systems. I have seen how this innovation benefits industries by improving overall system performance and cutting energy costs.
The design of low-pressure drop valves focuses on optimizing internal flow paths. By minimizing turbulence and resistance, these valves ensure smooth fluid movement. This design not only conserves energy but also extends the lifespan of hydraulic components by reducing wear and tear. For example, digital hydraulic valve configurations have been refined over the years to achieve lower pressure drops, making them ideal for energy-conscious applications.
Ningbo Hanshang Hydraulic Co., Ltd. integrates these advancements into our manufacturing processes. Our state-of-the-art facilities enable us to produce valves with precise flow characteristics, ensuring minimal energy loss. By adopting low-pressure drop designs, we support industries in their transition toward more sustainable operations.
“Small changes in valve design can lead to significant energy savings, proving that innovation lies in the details.”
Energy efficiency is no longer optional in hydraulic systems. It has become a necessity for industries aiming to reduce costs and meet environmental standards. By focusing on reducing power consumption and developing low-pressure drop valves, we contribute to a future where hydraulic systems are both efficient and sustainable.
Digital Twin Technology in Hydraulic Valve Manufacturing
Digital twin technology has emerged as a transformative force in hydraulic valve manufacturing. By creating virtual replicas of physical systems, this innovation bridges the gap between design and real-world performance. I have seen how this technology enhances efficiency and precision, making it indispensable for modern manufacturing processes.
Real-Time Replication of Hydraulic Systems
Digital twins enable real-time replication of hydraulic systems, offering unparalleled insights into their operation. These virtual models simulate the behavior of hydraulic valves under various conditions, providing accurate data for analysis. For instance, Computational Fluid Dynamics (CFD) software integrates seamlessly with digital twin systems. This integration collects real-time pressure data from valves and runs simulations instantly. The result is high-precision information that helps engineers refine designs and optimize performance.
I believe this capability revolutionizes how manufacturers approach problem-solving. Instead of relying on trial-and-error methods, engineers can predict system behavior and address potential issues before they arise. This proactive approach reduces downtime and ensures consistent performance. At Ningbo Hanshang Hydraulic Co., Ltd., we leverage advanced technologies to stay ahead in the competitive market. Our commitment to innovation reflects the broader industry trend toward adopting digital twin solutions.
“Digital twins transform data into actionable insights, empowering manufacturers to make informed decisions.”
The top 10 Industrial hydraulic valve factory leaders have embraced this technology to enhance their operations. By replicating hydraulic systems digitally, they achieve greater accuracy and reliability. This innovation aligns with the industry’s push for smarter and more efficient manufacturing practices.
Optimizing Performance and Maintenance
Digital twin technology plays a crucial role in optimizing performance and maintenance. By continuously monitoring hydraulic systems, these virtual models identify inefficiencies and suggest improvements. For example, digital twins analyze flow rates, pressure drops, and temperature variations in real time. This analysis helps engineers fine-tune valve designs to achieve optimal performance.
Predictive maintenance is another significant advantage. Digital twins detect early signs of wear and tear, allowing manufacturers to address issues before they escalate. This approach minimizes unexpected breakdowns and extends the lifespan of hydraulic components. I have observed how this technology reduces maintenance costs while improving system reliability. At Ningbo Hanshang Hydraulic Co., Ltd., we prioritize precision and durability in our products. By adopting digital twin solutions, we ensure that our hydraulic valves meet the highest standards of quality.
“Maintenance shifts from reactive to proactive with digital twin technology, saving time and resources.”
The integration of digital hydraulics further enhances the capabilities of digital twins. On/off valves convert digital signals into flow signals, combining information processing with hydraulic control. This innovation aligns perfectly with Industry 4.0, where connectivity and automation drive progress. I believe that digital twin technology will continue to shape the future of hydraulic valve manufacturing, offering new possibilities for efficiency and sustainability.
Globalization and Supply Chain Optimization in Hydraulic Valve Factories
Sourcing Materials and Components Globally
Globalization has reshaped the way hydraulic valve factories operate. I have observed that sourcing materials and components from around the world has become a standard practice. This approach allows manufacturers to access high-quality resources at competitive prices. For example, many factories procure precision-engineered components from regions known for their expertise in specific materials, such as Europe for advanced alloys or Asia for cost-effective electronic parts.
The top 10 Industrial hydraulic valve factory leaders have embraced this global strategy to remain competitive. By diversifying their supply chains, they reduce dependency on a single region and mitigate risks associated with disruptions. This flexibility ensures consistent production even during global challenges, such as material shortages or logistical delays.
I believe that sourcing globally also fosters innovation. Manufacturers gain exposure to cutting-edge technologies and practices from different regions. For instance, the rising demand for electro-hydraulic servo valves, projected to reach $1.42 billion by 2030, has driven factories to collaborate with suppliers specializing in digital electronics. This collaboration accelerates the development of intelligent and interconnected valves, meeting the evolving needs of industries like robotics and oil and gas.
At Ningbo Hanshang Hydraulic Co., Ltd., we prioritize sourcing materials and components from trusted global suppliers. Our commitment to quality ensures that every hydraulic valve we produce meets the highest standards. By leveraging a global supply chain, we deliver reliable and innovative solutions to our customers.
“A strong supply chain is the backbone of modern manufacturing. It connects innovation with execution.”
Streamlining Manufacturing Processes for Cost Efficiency
Streamlining manufacturing processes has become essential for hydraulic valve factories aiming to optimize costs. I have seen how factories adopt advanced technologies and lean practices to enhance efficiency. For instance, automation plays a significant role in reducing manual labor and minimizing errors. CNC digital lathes and high-precision grinding machines, like those used at Ningbo Hanshang Hydraulic Co., Ltd., ensure consistent quality while speeding up production.
Factories also focus on reducing waste to lower costs. Additive manufacturing, or 3D printing, has gained traction as a cost-effective method for producing complex components. This technology minimizes material usage and shortens production cycles. By integrating such innovations, manufacturers achieve significant savings without compromising quality.
Another key strategy involves implementing ERP systems to streamline operations. These systems provide real-time insights into inventory, production schedules, and supply chain activities. I have noticed how this transparency helps factories identify inefficiencies and make data-driven decisions. For example, optimizing production schedules reduces downtime and ensures timely delivery of products.
The emphasis on cost efficiency aligns with the industry’s competitive landscape. Manufacturers must balance affordability with quality to meet customer expectations. At Ningbo Hanshang Hydraulic Co., Ltd., we continuously refine our processes to deliver value-driven solutions. Our state-of-the-art facilities and commitment to excellence position us as a leader in the hydraulic valve industry.
“Efficiency is not just about cutting costs; it is about creating value through smarter processes.”
Increased Focus on Customization in Hydraulic Valve Manufacturing
Tailored Solutions for Specific Industry Needs
Customization has become a cornerstone of hydraulic valve manufacturing. I have observed that industries like oil and gas, chemical processing, and metalworking demand valves tailored to their unique operational requirements. Each sector presents distinct challenges, such as extreme temperatures, high pressures, or corrosive environments. Standardized solutions often fail to meet these specialized needs.
To address this, manufacturers now design valves with specific applications in mind. For example, the oil and gas industry requires valves capable of withstanding high-pressure drilling operations. In contrast, the chemical sector prioritizes corrosion-resistant materials to handle aggressive fluids. By tailoring products to these demands, manufacturers ensure optimal performance and reliability.
At Ningbo Hanshang Hydraulic Co., Ltd., we prioritize customization to meet diverse industry needs. Our advanced CNC digital lathes and high-precision machining centers enable us to produce valves with exact specifications. This capability allows us to deliver solutions that align perfectly with the operational goals of our clients.
“Customization is not just a feature; it is a necessity for industries striving for efficiency and precision.”
The growing emphasis on tailored solutions reflects a broader trend in industrial manufacturing. Companies now recognize that one-size-fits-all approaches no longer suffice. By focusing on customization, manufacturers enhance their competitiveness and build stronger relationships with their clients.
Flexible Manufacturing Processes to Meet Demand
Flexibility in manufacturing processes has become essential for meeting the rising demand for customized hydraulic valves. I have seen how traditional production methods struggle to adapt to the rapid changes in market requirements. Modern factories now adopt advanced technologies to ensure agility and efficiency.
One key strategy involves the use of modular designs. By standardizing certain components, manufacturers can quickly assemble customized valves without starting from scratch. This approach reduces lead times and lowers production costs. For instance, modular valve systems allow for easy configuration changes, enabling manufacturers to cater to various industries with minimal adjustments.
Automation also plays a crucial role in enhancing flexibility. At Ningbo Hanshang Hydraulic Co., Ltd., we utilize state-of-the-art equipment, including high-precision grinding machines and honing machines. These tools streamline production and ensure consistent quality, even for complex designs. Our ERP administration model further optimizes operations by providing real-time insights into inventory and production schedules.
“Flexibility in manufacturing is the key to staying ahead in a dynamic market.”
The adoption of flexible processes benefits both manufacturers and clients. Companies can respond quickly to changing demands, while clients receive products that meet their exact specifications. This adaptability has become a defining characteristic of leading hydraulic valve manufacturers.
By focusing on customization and flexibility, the hydraulic valve industry continues to evolve. These trends not only address the unique needs of various sectors but also drive innovation and efficiency. At Ningbo Hanshang Hydraulic Co., Ltd., we remain committed to delivering tailored solutions through advanced and adaptable manufacturing practices.
The top 10 trends in industrial hydraulic valve manufacturing highlight the industry’s commitment to innovation and sustainability. From IoT integration and miniaturization to advanced simulation software and eco-friendly practices, these developments redefine efficiency and precision. Manufacturers now leverage technologies like AI and 3D printing to meet the growing demand for smart, customized solutions across industries such as robotics, aerospace, and oil & gas.
“Sustainability and innovation are no longer optional—they are essential for growth.”
I encourage manufacturers to embrace these trends. By doing so, they can enhance competitiveness, reduce costs, and contribute to a greener future while meeting the evolving needs of modern industries.