Key Takeaways
- Counterbalance valves are essential for maintaining load stability in hydraulic systems, preventing uncontrolled movements and enhancing safety.
- By reducing pressure pulsations and effector oscillations, counterbalance valves improve the efficiency and precision of hydraulic operations.
- Selecting the right type of counterbalance valve based on your system’s specific needs is crucial for optimal performance and safety.
- Regular testing and maintenance of counterbalance valves are vital to ensure their functionality and prolong the lifespan of your hydraulic equipment.
- Implementing counterbalance valves can lead to significant cost savings by reducing downtime, maintenance expenses, and improving overall productivity.
- Counterbalance valves allow for controlled lowering of loads, enhancing safety and efficiency in various applications, from construction to manufacturing.
Understanding Load Control Issues
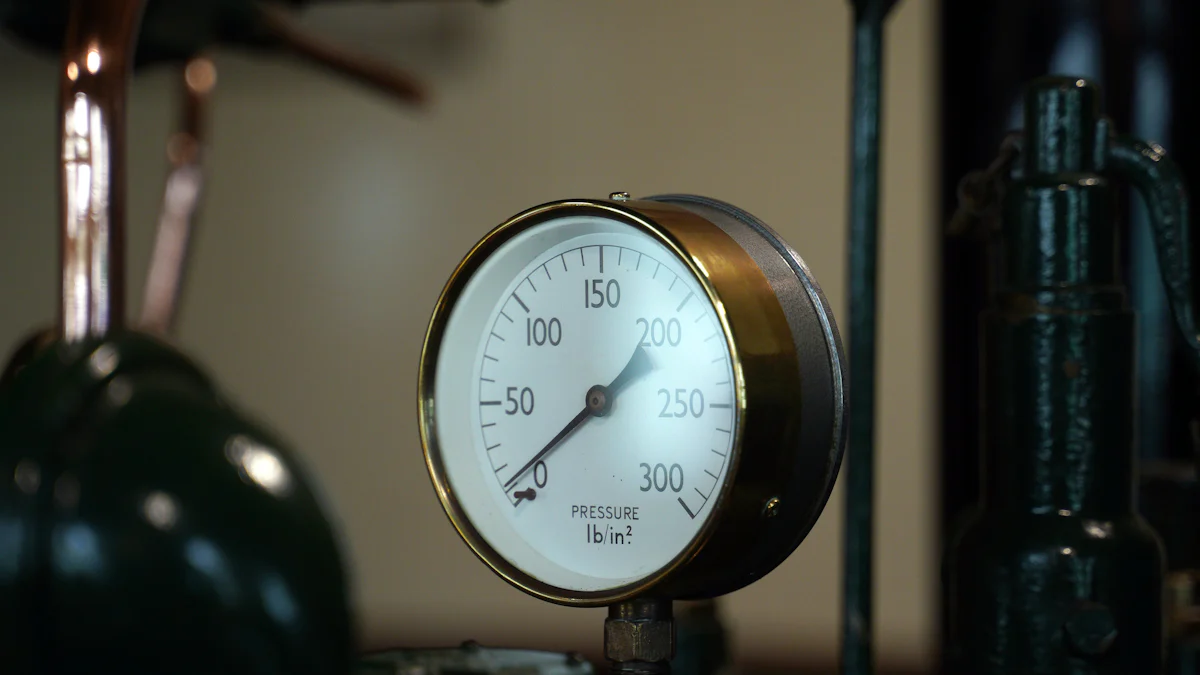
Definition and Significance
Load control issues in hydraulic systems refer to the challenges you face when managing the movement and stability of loads. These issues arise when the system struggles to maintain control over the load, leading to inefficiencies and potential safety hazards. Proper load control is crucial because it ensures that your machinery operates smoothly and safely. By addressing these issues, you enhance the precision and reliability of your equipment, which is vital for maintaining productivity and reducing downtime.
Common Problems in Hydraulic Systems
Hydraulic systems often encounter several common problems that affect load control. One major issue is pressure pulsations, which can cause erratic movements and reduce the accuracy of your operations. These pulsations occur when there is an imbalance in the hydraulic fluid flow, leading to fluctuations in pressure levels. Another problem is effector oscillations, where the working tool or component experiences unwanted vibrations. This can result in tool deviations and impact the quality of your work.
Downtime between work cycles is another challenge you might face. When your system takes longer to stabilize between operations, it leads to inefficiencies and increased operational costs. Additionally, line pressures can spike unexpectedly, causing oil to leave the cylinder holding a load. This not only affects stability but also poses a risk to the safety of your equipment and personnel.
Counterbalance valves, also known as load-holding valves, play a crucial role in addressing these issues. They act as adjustable pressure relief valves, preventing oil from leaving the cylinder and maintaining load stability. By incorporating counterbalance valves into your hydraulic systems, you can significantly improve stability, reduce pressure pulsations, and minimize downtime. This makes them an essential component for anyone looking to optimize their hydraulic operations.
What are Counterbalance Valves?
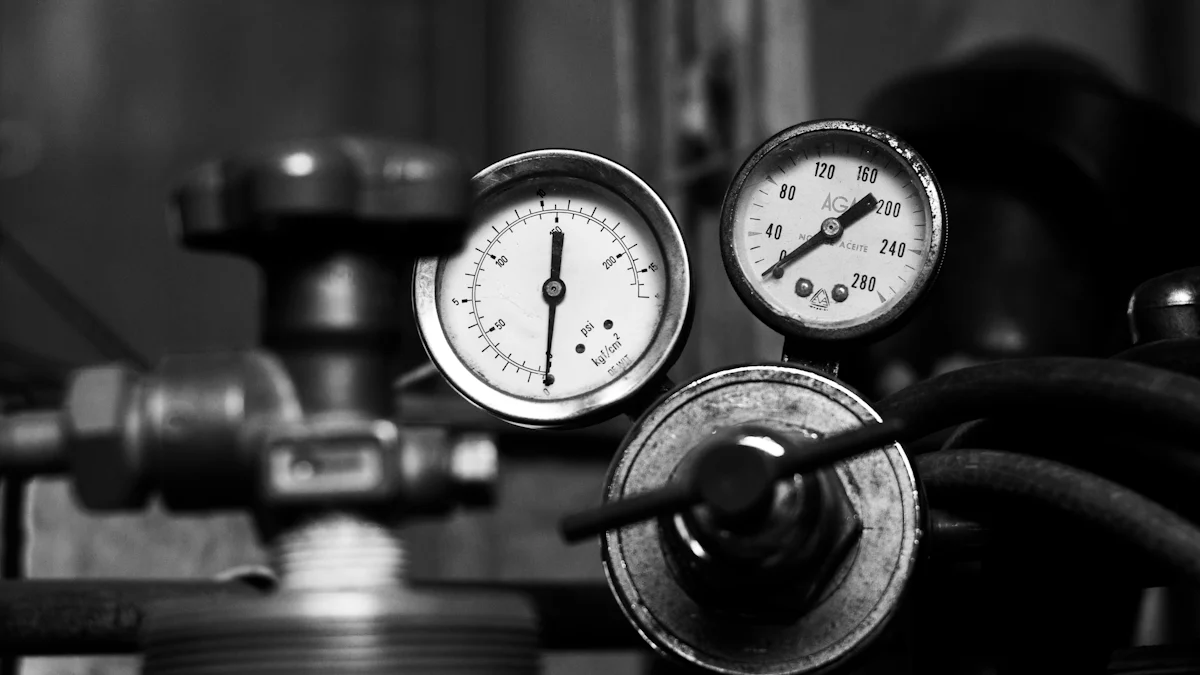
Definition and Role
Counterbalance valves serve as essential components in hydraulic systems, ensuring controlled and stable load movements. You use these valves to prevent uncontrolled movements of cylinders and motors, especially when dealing with suspended loads. By acting as adjustable pressure relief valves, counterbalance valves maintain a back-pressure in the hydraulic circuit. This back-pressure prevents oil from leaving the cylinder, thus holding the load securely even if oil pressure drops unexpectedly. In essence, they provide a counterforce to sustain loads in vertical or inclined positions, reducing the influence of gravity or inertia.
When you incorporate counterbalance valves into your system, you achieve smooth and consistent control over load movements. These valves open at a point of equilibrium, allowing the load to lower at a velocity dictated by the pump flow rate rather than mass and gravity. This feature makes them indispensable for applications requiring precise load control and safety.
Types of Counterbalance Valves
Counterbalance valves come in various types, each designed to meet specific operational needs. The most common types include:
-
Standard Counterbalance Valves: These valves are typically used in conjunction with hydraulic cylinders to hold suspended loads safely. They also control load movement and prevent pressure spikes in the line where they are installed.
-
Brake Valves: When used with hydraulic motors, counterbalance valves are often referred to as brake valves. They control runaway loads caused by mass or gravity, ensuring smooth and safe operations.
-
Triple Ratio Counterbalance Valves: This innovative type offers enhanced stability and efficiency. It uses a low pilot ratio for stability when needed and a higher pilot ratio when the cylinder doesn’t move yet. This design allows for lower inlet pressures while maintaining the same speed, making it a more efficient option compared to standard counterbalance valves.
By selecting the appropriate type of counterbalance valve, you can optimize your hydraulic system’s performance, ensuring both safety and efficiency.
How Counterbalance Valves Solve Load Control Issues
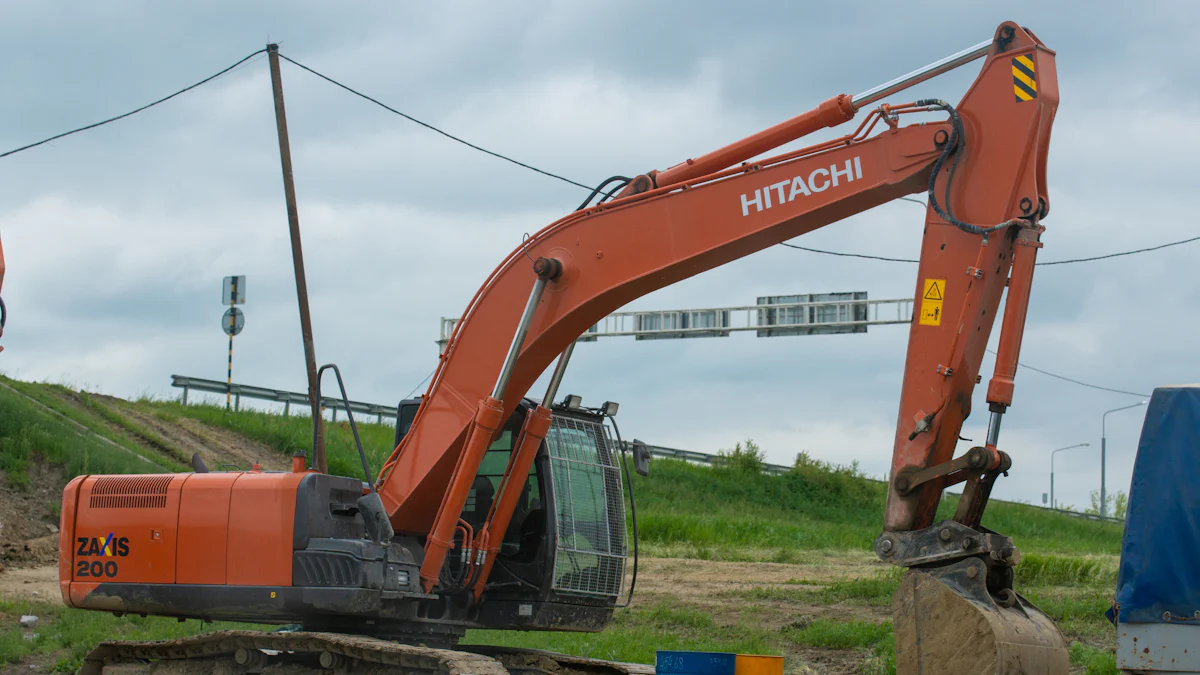
Mechanisms of Action
Counterbalance valves play a pivotal role in hydraulic systems by ensuring precise load control. They achieve this through specific mechanisms that enhance stability and prevent unwanted movements.
Maintaining Stability
You can rely on counterbalance valves to maintain stability in your hydraulic systems. These valves generate counterforces that counteract the effects of gravity and inertia. By doing so, they prevent overrunning loads and ensure smooth operations. When you use a counterbalance valve, it maintains a set pressure within the system. This pressure acts as a stabilizing force, holding the load securely in place. As a result, you experience improved precision and reduced pressure pulsations, which are crucial for maintaining the accuracy of your hydraulic manipulator.
Preventing Free Fall
Preventing free fall is another critical function of counterbalance valves. When you deal with suspended loads, the risk of uncontrolled descent is significant. Counterbalance valves address this by acting as thermal relief valves. They prevent oil from leaving the cylinder unexpectedly, thus avoiding sudden drops. By controlling the flow of hydraulic fluid, these valves ensure that the load lowers at a controlled rate. This mechanism not only enhances safety but also improves the efficiency of your operations.
Examples of Application
Counterbalance valves find applications in various industries due to their ability to control loads effectively. In construction equipment, you use these valves to manage the movement of heavy machinery components. They ensure that cranes and excavators operate smoothly, preventing sudden jerks or drops. In the manufacturing sector, counterbalance valves enhance the precision of robotic arms and hydraulic presses. By maintaining consistent pressure, they improve the quality of the final product.
In the automotive industry, counterbalance valves are essential for controlling the movement of car lifts and other hydraulic tools. They provide the necessary stability to ensure safe and efficient operations. Additionally, you can find these valves in agricultural machinery, where they help manage the movement of plows and harvesters. By incorporating counterbalance valves into your hydraulic systems, you can achieve better control, enhanced safety, and improved efficiency across various applications.
Steps to Implement Counterbalance Valves
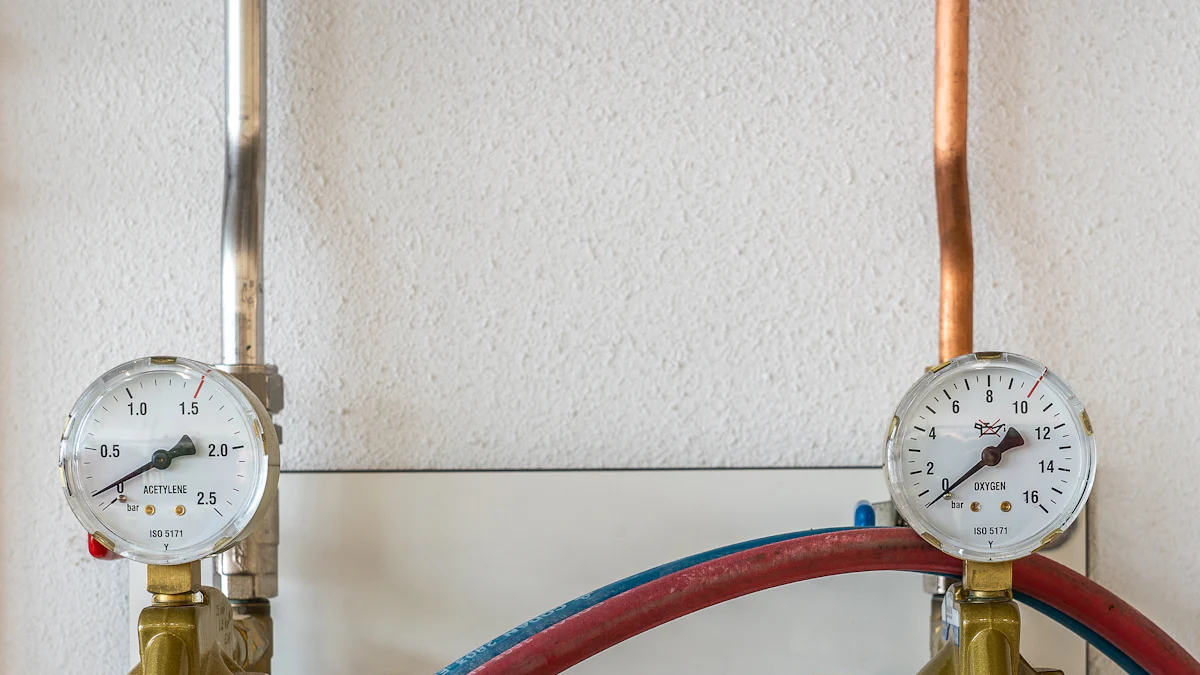
Implementing counterbalance valves in your hydraulic system involves several critical steps. By following these steps, you can ensure optimal performance and safety.
Assessing System Requirements
Begin by evaluating your hydraulic system’s specific needs. Identify the types of loads you handle and the operational conditions. Consider factors such as load weight, speed, and the potential for runaway loads. Understanding these elements helps you determine the necessary specifications for your counterbalance valves.
“Counterbalance valves aid in the safe and dynamically balanced lowering of loads at a velocity dictated by the pump flow rate and not mass and gravity.”
This assessment ensures that you select a valve that meets your system’s demands, providing stability and control.
Selecting the Right Valve
Choose a counterbalance valve that aligns with your system’s requirements. Consider the valve’s flow rating, pressure capacity, and pilot ratio. These features influence the valve’s ability to manage load movements effectively. For instance, a high flow rating conserves energy while maintaining control at low flow rates.
“Command Controls’ counterbalance valves have no dynamic seals, so they are virtually free of hysteresis.”
Opt for valves with advanced designs that eliminate dynamic seals, reducing hysteresis and enhancing responsiveness. This choice minimizes issues like bounce and chatter, ensuring smooth operations.
Installation Process
Proceed with the installation of the selected counterbalance valve. Position the valve correctly within the hydraulic circuit to manage load movements efficiently. Ensure that trained hydraulic personnel perform the setup to avoid errors. Adjust the valve’s settings to match the load-induced pressure, typically 30% above the maximum load pressure. This adjustment allows the valve to reseat properly and prevents runaway loads.
“The valve does need to be readjusted when loads change, but this is a small price to pay for good control.”
During installation, verify that the valve opens fully when pressure at the actuator inlet increases. This feature ensures smooth load lowering and enhances system safety. Regularly inspect and maintain the valve to sustain its performance over time.
By following these steps, you can successfully implement counterbalance valves in your hydraulic systems, achieving improved control and efficiency.
Testing and Maintenance
Testing and maintaining counterbalance valves are crucial steps to ensure your hydraulic system operates efficiently and safely. Regular checks and upkeep help you avoid unexpected failures and prolong the lifespan of your equipment.
1. Initial Testing
After installing a counterbalance valve, conduct an initial test to verify its functionality. Begin by checking the valve’s response to load changes. Ensure that it maintains stability and prevents runaway loads. Observe the valve’s ability to open fully when pressure at the actuator inlet increases. This feature is vital for smooth load lowering and system safety.
2. Routine Inspections
Schedule routine inspections to monitor the valve’s performance. Look for signs of wear or damage, such as leaks or unusual noises. Pay attention to the valve’s response time and ensure it follows the control signals accurately. A well-functioning valve should eliminate bounce, loud chatter, and high-pitch squealing, providing smooth and quiet operations.
3. Adjustments and Calibration
Adjust the valve settings as needed to match changes in load conditions. Set the adjustable springs at least 30% above the maximum induced load pressure. This adjustment allows the valve to reseat properly and prevents runaway loads. Regular calibration ensures the valve maintains optimal performance and adapts to varying operational demands.
“Counterbalance valves have adjustable springs and should be set at least 30% over the maximum induced load pressure to allow the valve to reseat properly.”
4. Maintenance Practices
Implement a maintenance routine to keep the valve in top condition. Clean the valve components regularly to prevent contamination and ensure smooth operation. Replace worn-out parts promptly to avoid compromising the system’s efficiency. By maintaining the valve, you reduce downtime and enhance the overall reliability of your hydraulic system.
5. Performance Evaluation
Evaluate the valve’s performance periodically to assess its impact on the hydraulic system. Monitor the precision and dynamics of load movements, especially during high-speed operations. Counterbalance valves should reduce pressure pulsations and effector oscillations, leading to improved accuracy and reduced downtime.
By following these testing and maintenance steps, you ensure that your counterbalance valves function effectively, providing stability and control in your hydraulic systems. Regular upkeep not only enhances safety but also optimizes the efficiency of your operations.
Benefits of Using Counterbalance Valves
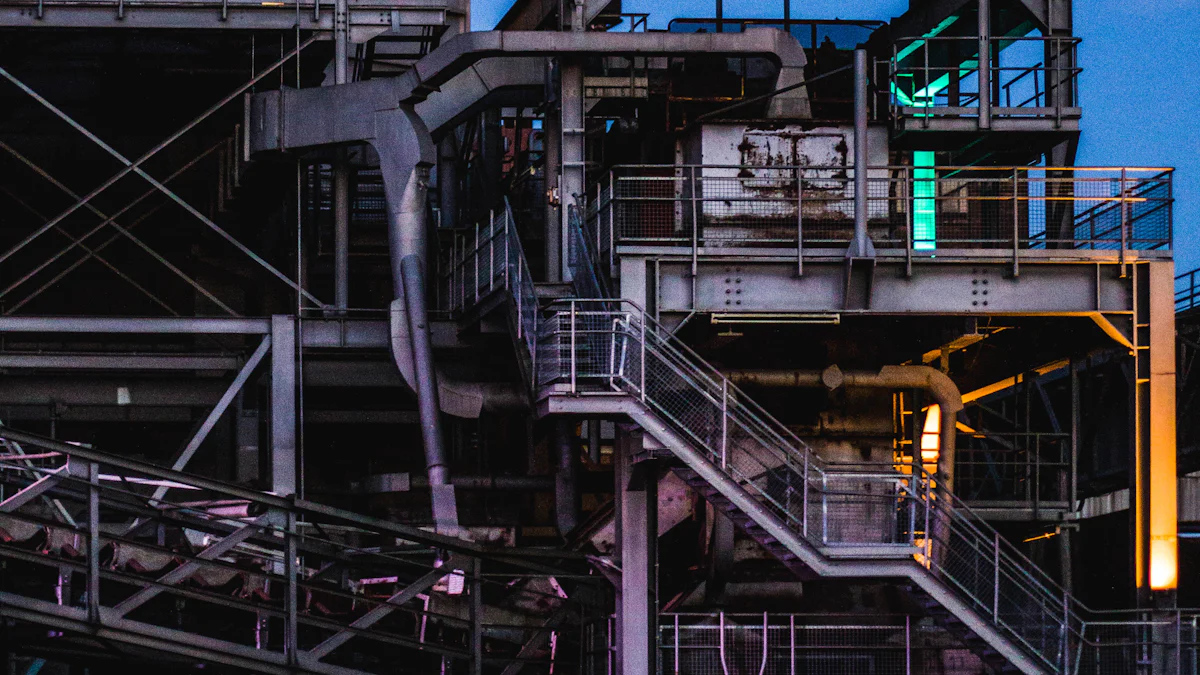
Improved Safety
You enhance safety in hydraulic systems by using counterbalance valves. These valves prevent runaway loads, ensuring stable movement of cylinders and motors. When loads transfer from compression to tension, the risk of uncontrolled movements increases. Counterbalance valves mitigate this risk by maintaining a controlled flow of hydraulic fluid. This control prevents sudden drops or jerks, protecting both equipment and personnel from potential hazards. By incorporating these valves, you create a safer working environment, reducing the likelihood of accidents and equipment damage.
Enhanced Efficiency
Counterbalance valves significantly boost the efficiency of hydraulic systems. They reduce pressure pulsations and effector oscillations, leading to smoother operations. When you use these valves, you minimize energy consumption, as they allow for precise control over load movements. This precision reduces the wear and tear on your equipment, extending its lifespan and lowering maintenance costs. In applications where high-speed movements are essential, counterbalance valves ensure that your machinery operates at optimal performance levels, enhancing overall productivity.
Cost-Effectiveness
Investing in counterbalance valves proves cost-effective in the long run. By improving safety and efficiency, these valves reduce downtime and maintenance expenses. You avoid costly repairs and replacements by preventing equipment damage and minimizing operational disruptions. Additionally, the enhanced control provided by counterbalance valves leads to better quality outputs, reducing waste and rework. Over time, the initial investment in these valves pays off through increased productivity and reduced operational costs, making them a smart choice for any hydraulic system.
In summary, counterbalance valves offer a robust solution for managing load control issues in hydraulic systems. They provide stability and efficiency by maintaining set pressure against loads and preventing uncontrolled movements. These valves excel in controlling runaway loads caused by mass or gravity, ensuring smooth operations across varying speeds and loads. By incorporating counterbalance valves, you enhance safety, reduce downtime, and improve the overall performance of your hydraulic systems. Their unique design and functionality make them an indispensable component for optimizing hydraulic operations.
FAQ
What is the primary function of counterbalance valves?
Counterbalance valves primarily prevent uncontrolled movements in hydraulic systems. They generate a counterforce to sustain loads in vertical or inclined positions, ensuring stability and safety. By acting as adjustable pressure relief valves, they maintain control over load movements and prevent pressure spikes.
How do counterbalance valves enhance efficiency in hydraulic systems?
You can enhance efficiency by using counterbalance valves, which reduce pressure pulsations and effector oscillations. This leads to smoother operations and improved precision. The valves ensure that hydraulic manipulators operate with greater accuracy, minimizing downtime and boosting productivity.
Why are counterbalance valves crucial for hydraulic systems?
Counterbalance valves are essential because they maintain stability and efficiency. They prevent over-running loads and ensure controlled lowering of loads. This control is vital for maintaining the safety and reliability of hydraulic systems, especially in applications involving suspended loads.
Can counterbalance valves improve the performance of mobile equipment?
Yes, counterbalance valves, also known as load-holding valves, significantly improve the performance of mobile machines. They enhance stability and reduce operational costs by preventing uncontrolled movements and maintaining safe load handling.
What types of hydraulic systems benefit most from counterbalance valves?
Hydraulic systems that handle suspended loads or require precise load control benefit the most. These include construction equipment, manufacturing machinery, automotive tools, and agricultural machinery. Counterbalance valves ensure these systems operate smoothly and safely.
How do counterbalance valves contribute to cost-effectiveness?
By improving safety and efficiency, counterbalance valves reduce downtime and maintenance expenses. They prevent equipment damage and minimize operational disruptions, leading to lower repair costs. Over time, the investment in these valves results in increased productivity and reduced operational costs.
Are there different types of counterbalance valves?
Yes, there are various types, including standard counterbalance valves, brake valves, and triple ratio counterbalance valves. Each type serves specific operational needs, allowing you to choose the most suitable option for your hydraulic system’s requirements.
How do counterbalance valves ensure safe load lowering?
Counterbalance valves ensure safe load lowering by controlling the flow of hydraulic fluid. They act as thermal relief valves, preventing oil from leaving the cylinder unexpectedly. This control allows loads to lower at a controlled rate, enhancing safety and efficiency.
What should you consider when selecting a counterbalance valve?
When selecting a counterbalance valve, consider factors like flow rating, pressure capacity, and pilot ratio. These features influence the valve’s ability to manage load movements effectively. Choose a valve that aligns with your system’s specific requirements for optimal performance.
How often should you maintain counterbalance valves?
Regular maintenance is crucial for ensuring optimal performance. Conduct routine inspections, adjust settings as needed, and replace worn-out parts promptly. Regular upkeep not only enhances safety but also optimizes the efficiency of your hydraulic systems.